The Scientific Research Behind Porosity: A Comprehensive Overview for Welders and Fabricators
Comprehending the detailed systems behind porosity in welding is crucial for welders and makers aiming for impeccable workmanship. As metalworkers look into the depths of this sensation, they reveal a globe governed by different variables that affect the development of these tiny voids within welds. From the structure of the base products to the intricacies of the welding process itself, a plethora of variables conspire to either worsen or relieve the visibility of porosity. In this extensive guide, we will untangle the scientific research behind porosity, exploring its effects on weld top quality and unveiling progressed methods for its control. Join us on this journey with the microcosm of welding flaws, where accuracy satisfies understanding in the search of remarkable welds.
Recognizing Porosity in Welding
FIRST SENTENCE:
Assessment of porosity in welding reveals critical insights right into the integrity and high quality of the weld joint. Porosity, identified by the existence of cavities or voids within the weld metal, is a typical worry in welding procedures. These voids, otherwise correctly addressed, can endanger the architectural honesty and mechanical residential properties of the weld, causing prospective failings in the completed item.
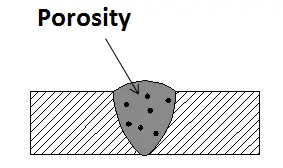
To discover and evaluate porosity, non-destructive screening methods such as ultrasonic testing or X-ray examination are typically utilized. These methods permit for the identification of interior flaws without compromising the honesty of the weld. By analyzing the size, shape, and distribution of porosity within a weld, welders can make enlightened choices to enhance their welding processes and achieve sounder weld joints.
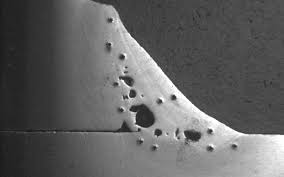
Variables Affecting Porosity Formation
The occurrence of porosity in welding is influenced by a myriad of factors, ranging from gas shielding performance to the ins and outs of welding criterion setups. One essential element adding to porosity formation is inadequate gas securing. When the protecting gas, normally argon or carbon dioxide, is not properly covering the weld swimming pool, climatic gases like oxygen and nitrogen can infect the molten metal, leading to porosity. Additionally, the cleanliness of the base materials plays a substantial role. Impurities such as rust, oil, or moisture can vaporize throughout welding, producing gas Click Here pockets within the weld. Welding specifications, including voltage, current, take a trip speed, and electrode kind, likewise impact porosity development. Using inappropriate settings can create extreme spatter or heat input, which in turn can cause porosity. The welding strategy employed, such as gas steel arc welding (GMAW) or secured metal arc welding (SMAW), can affect porosity formation due to variations in warmth distribution and gas protection. Understanding and controlling these More about the author aspects are essential for lessening porosity in welding procedures.
Results of Porosity on Weld High Quality
Porosity development considerably compromises the structural integrity and mechanical residential or commercial properties of bonded joints. When porosity exists in a weld, it develops gaps or cavities within the material, minimizing the total strength of the joint. These voids function as stress concentration points, making the weld a lot more at risk to breaking and failure under lots. The presence of porosity likewise deteriorates the weld's resistance to deterioration, as the entraped air or gases within deep spaces can react with the surrounding atmosphere, causing deterioration in time. Furthermore, porosity can impede the weld's capability to stand up to stress or effect, additional endangering the general high quality and dependability of the bonded structure. In important applications such as aerospace, vehicle, or architectural buildings, where safety and resilience are paramount, the detrimental results of porosity on weld top quality can have extreme effects, highlighting the value of decreasing porosity through correct welding methods and procedures.
Strategies to Reduce Porosity
In addition, making use of the ideal welding criteria, such as the correct voltage, current, and take a trip rate, is essential in preventing porosity. Maintaining a constant arc length and angle during welding also aids lower the probability of porosity.

Making use of the ideal welding method, such as back-stepping or using a weaving motion, can additionally aid disperse Related Site warm evenly and lower the possibilities of porosity development. By executing these methods, welders can efficiently decrease porosity and create top quality bonded joints.
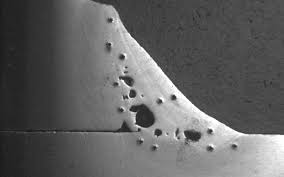
Advanced Solutions for Porosity Control
Applying cutting-edge innovations and innovative techniques plays a crucial role in accomplishing premium control over porosity in welding processes. Furthermore, using advanced welding methods such as pulsed MIG welding or changed environment welding can additionally aid reduce porosity problems.
An additional advanced service includes making use of innovative welding equipment. Making use of equipment with built-in features like waveform control and advanced power sources can improve weld high quality and minimize porosity dangers. In addition, the execution of automated welding systems with specific control over parameters can considerably reduce porosity problems.
Additionally, integrating advanced monitoring and inspection modern technologies such as real-time X-ray imaging or automated ultrasonic screening can assist in identifying porosity early in the welding procedure, enabling prompt rehabilitative activities. On the whole, incorporating these innovative options can significantly boost porosity control and improve the total quality of bonded components.
Final Thought
Finally, recognizing the scientific research behind porosity in welding is necessary for welders and producers to create top quality welds. By determining the factors affecting porosity formation and applying techniques to lessen it, welders can improve the total weld high quality. Advanced remedies for porosity control can additionally boost the welding procedure and ensure a strong and trusted weld. It is crucial for welders to continuously educate themselves on porosity and apply finest practices to accomplish optimal outcomes.
Comments on “What is Porosity in Welding: Necessary Tips for Getting Flawless Welds”